By Sabrina Beck
Is brushing all you need to do to clean and protect your teeth and gums? No. Just like batch technology is no longer enough to clean your printed circuit boards.
Brushing your teeth removes plaque buildup from the front and back surfaces of teeth. But to fully clean and protect teeth you need to floss so you remove plaque from between teeth and underneath your gums. In May 2017 Altek made an advancement in PCB cleaning, rinsing, and drying that’s similar to switching from just brushing the surface of your teeth to brushing and flossing in between the tight spaces of the teeth.
As of May, 2017 Altek has the capability of cleaning, rinsing, and drying PCBs with the latest inline technology. From the Technical Devices Company, Altek purchased a Nu/Clean 800 Series inline aqueous cleaner.
Throughout the PCB industry, assemblers face a daunting and growing challenge. Today’s PCBs feature much greater density, complexity, and miniaturization. Tomorrow’s PCBs will be even harder to clean. The narrowing space between components and boards makes thoroughly cleaning them increasingly difficult. Board assemblers who currently clean with a batch-type cleaner are looking for solutions to increase cleaning capability. Altek has found the solution.
The Altek plant now features a three foot wide, 25 foot long industrial “washing machine.” A main feature of this Nu/Clean machine is its flood box technology.
Flood Box Technology
The machine’s flood box technology involves a “bathtub” with water jets that soak the boards and agitate the flux residues to clean underneath low standoff components. The circuit boards are submerged completely, so no area is missed. Because the boards are neither lowered nor raised there’s no jarring or potential to dislodge or damage components on the conveyor. A trip through the flood box combines a pressurized spray from nozzles with a flood of turbulent fluid. The next step is conventional top and bottom spray bars. Along with the rinsing and drying features, these cleaning features provide at least five major benefits to Altek clients.
Penetrating and Cleaning Despite Lower Clearances
Industry research finds that this type of inline aqueous cleaning provides greater penetration of low clearances within the electronic assembly. The new equipment technology is effective at cleaning both flux residues and ionic contamination under the body of the component. The soaking action of the cleaning agent on the surface of the printed circuit board softens the flux residue. When that residue gets bombarded with the pressurized spray, the residue floats free from the PCB. And because the cleaning agent pools onto the board, it lowers surface tension, helping to penetrate under tightly spaced components.
Reducing the Potential of Unwanted Removals
Another key feature—reduced coherent spray jets—provides protection against dislodging labels, removing part marking, or negatively impacting board components. Coherent spray jets deliver the cleaning agent at higher pressures onto the printed circuit board. The pressurized spray jets provide strong deflective forces for penetrating and moving the cleaning agent under the component. But having too many spray jets or too strong of a stream can undercut labels, remove part marking, and potentially affect other material compatibility effects. The Nu/Clean 800 at Altek uses fan sprays that reduce the impact to the electronic board. Fifteen stainless steel pumps give just the right balance of pressure and flow to remove residues and contaminants.
Rinsing More Thoroughly and Safely
The cleaning agent in the new equipment is attracted to water. With a layer of water covering the surface of each board within the rinse section, removal of the cleaning agent under bottom termination components is improved.
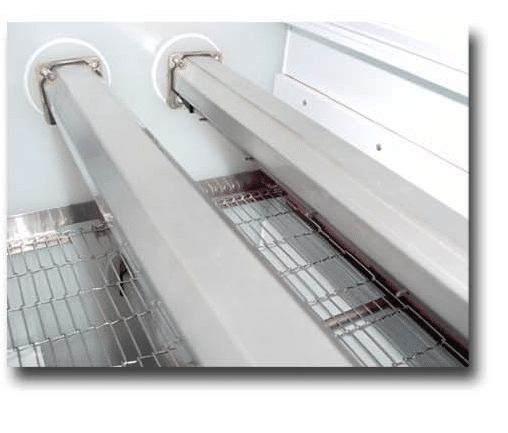
The double air curtain and anti-drag out zone is one of many features that reduces cost by saving chemicals
Becoming More Environmentally-friendly and Cost-effective
Cleaning More Boards Faster and More Completely with Less Human Touch
This new cleaning technology provides Altek with higher throughput. We can now clean more boards at a faster pace, enabling us to meet customers’ tight schedules. The reduction in human touch means there are fewer opportunities to introduce defects through human error.
Altek produces more than 500 different products for customers. The Nu/Clean has the flexibility to handle a wide variety of these products. And, to meet customer requirements, we can adjust many factors including temperature, conveyor speed, and pump pressure. Our first test run on May 2 demonstrated how this new technology will advance the cleanliness and effectiveness of customer’s circuit boards.
Your dentist knows a healthy mouth is a portal to a healthy body. Altek knows a great system for cleaning, rinsing, and drying circuit boards is a portal to delivering high performing, high quality PCBs.